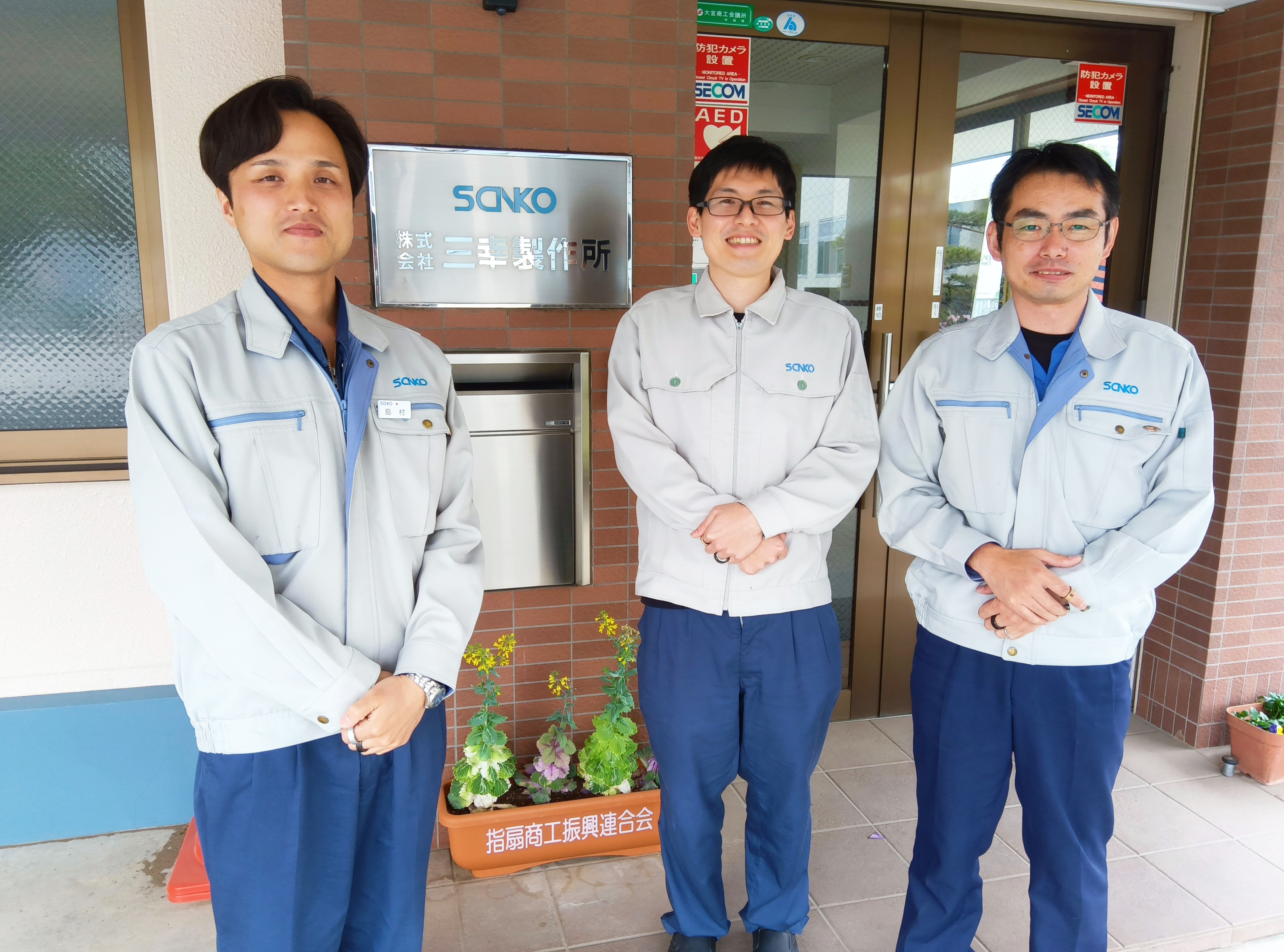
製造部 主任補佐 田中 (たなか)様(右)
製造部 主任補佐 島村 (しまむら)様(左)
- 検査表を社内郵便で数日かけて回付する承認フロー、急ぎの場合は担当者が走ることも
- プリザンターの導入によって紙資料の電子保存を実現、ドキュメントの検索性の高さに現場が感心
- 社内でプリザンターの活用が積極化し、開発が必要になれば認定パートナーに依頼する体制を構築
課題:保存義務のある製造検査の記録表が大量に積み上がり管理が困難
各部の承認を得るために従業員が社内を走って回るようなケースも
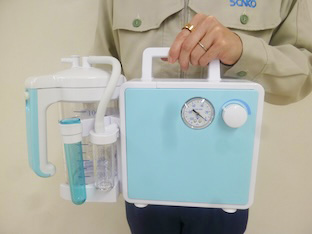
三幸製作所は埼玉県に工場を構える医療機器メーカーです。主力製品の吸引器(気道などに溜まった唾液や痰を吸い出して取り除く医療機器)では国内トップで6割のシェアを誇ります。医療機器の設計、開発から製造、メンテナンスまで一貫して行えることが強みです。
そうした中、同社では生産性を高めるため、数年前から業務のDX(デジタルトランスフォーメーション)を目標に掲げ、システムの導入を模索してきました。特に課題となっていたのが、製造の現場で紙資料による生産管理がいまだに残っていたことです。
例えば、医療機器は製造記録や検査記録を作成しなければなりません。それらの記録は法律で生産終了後15年間保存することが義務付けられています。同社では昔から紙で記録を作成しておりました。倉庫代わりとなる専用の部屋を確保し、現在2部屋で保管していますが、このままでは製品の種類が増えていくにつれて、倉庫の増設が必要なことは明らかです。「納品後、販売先から『この製品の検査報告書がほしい』と頼まれることも多くあります。そのたびに紙資料を保管庫から探さなければならず、手間がかかることに頭を痛めていました」と、同社品質保証部の池澤氏は話します。
さらに、問題となっていたのが、検査表をはじめとする紙資料に関して、各部署の承認を得るために、ハンコを押して記録を作成していたことです。検査表は製品出荷前に必ず責任者の承認が必要です。同社では敷地内にオフィスや工場が点在しており、社内郵便という流れで紙を回して承認を得るようにしていました。そのため、承認を見越した冗長な生産リードタイムになっていました。お客様の要望で納期を急がれた場合は、納品を早めるために従業員が“走って”承認に社内を回ることも余儀なくされていたのです。「時間をかけて紙で記録を作成しても、そこを喜ぶお客様は皆無。より付加価値の高い業務に集中するためにもデジタル化はまったなしの状況でした」(池澤氏)
システムの選定:コスト面で計画がとん挫する中、プリザンターが有力候補に浮上
入力と保存を分けたハイブリッドシステムで現場の抵抗を回避
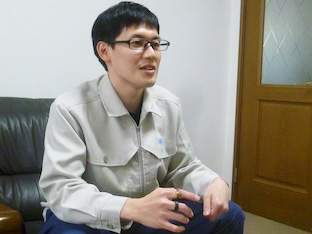
しかし、同社では検査記録のデジタル化に向けて様々な施策が出ては消えることを繰り返します。懸案となったのが費用です。
一時、医療機器業者に特化した文書管理クラウドサービスも検討しましたが、導入とランニングコストを合わせると年間費用が1000万円と高額な点がネックでした。その他、スクラッチでの構築、パッケージソフトのカスタマイズによる導入も考えましたが、いずれも高額になり、「DX化はお金がかかるんだな」と当初の予算に合わず実現に至らなかったのです。
そんな中、有力候補として浮上したのがプリザンターです。池澤氏が展示会に出展していたプリザンターの認定パートナーであるSMSデータテック(以下、SDT)のブースに立ち寄ったことがきっかけです。「検査表の電子化は問題なく可能と言われ、自分たちで簡単にカスタマイズできるという点も魅力でした。費用も従来の10分の1程度で済みます。プリザンターであれば遅々として進まないDXも一歩踏み出せるのではないかと考えました」(池澤氏)
池澤氏から依頼を受けて、別の方法で電子化の検討をしていたのが、製造部主任補佐の島村 氏です。初期段階として、紙の書類の様式を模して作成したExcel帳票をベースにWEBブラウザから現場で直接入力できる別サービスを開始してはどうかと提案しました。
「別サービスは従来のフォーマットと見た目が同様です。そのため使用者に抵抗がないのではないかと考えました」(島村氏)
その結果、導入テストとして、検査表の電子化は別サービスでスタートすることにしたのです。
「しかし、保存に関して不安があり、そこでプリザンターを活用できないかとSDTに相談をすることにしました」(島村氏)
そこで、提案をされたのが、入力と保管を分割する運用体制です。
内容は、別サービスで入力された検査表データをPDFとExcelで出力してプリザンターへドキュメントとして保存する方式です。
「これであれば入力作業は変わらないため、現場も抵抗なく使うことができ、システムの安定性も担保されます。ひとまずこの形を初期段階として導入し、運用を図ることで、当社のデジタル化の第一歩とすることにしたのです」(島村氏)
システムの導入:紙の運用が日常の社員にとってDXの利点に気付くきっかけとなったデジタルの検索性
社内でDXへの意識が高まり、電子化の相談が少しずつ舞い込む
早速、SDTはハイブリッド案に基づき、仮のデータを用いたデモ画面を作成しました。実際に操作してみて、島村氏は「率直に言って興奮した」と、当時を振り返ります。「検査表のデータをブラウザ上に直接入力し、出来上がったドキュメントがプリザンターに保存されたのを目の当たりにして、これでようやく紙によるアナログ運用から脱却できると期待が膨らみました」(島村氏)
そして、システムが本稼働し、現場ではデータを直接入力する運用がスタート。導入してはじめは覚えることがあって、前向きではなかった部分もありました。島村氏は実作業者が入力、保存した後、「試しに今作ったドキュメントをキーワードで検索してみてください」と伝え、操作を促します。その通りに操作すると、当該ドキュメントが表示され、それを見た実作業者は思わず「おぉっ」という感心の声を上げたのです。こうした反応を見て、システムは反発されずに定着していくという見通しが付いたのです」(島村氏)
システムが本稼働して、数日後、実作業者もすぐに慣れ「もう紙には戻れないね」という感想が寄せられました。
今まで時間がかかっていた承認もタイムリーに進めるようになり、生産性向上にもつながりました。承認をもらいに走っていた社員は、走る必要が無くなって太ってしまいました。
もちろん、紙が無くなったのでコピー用紙も削減、倉庫増設の必要もなくなりました。
製造部での記録の電子化が端緒について、事態は思わぬ方向に進展します。「今回導入したプリザンターというWEBデータベースは、様々な業務のデジタル化ができるらしい」という噂が社内で広まり、一人、また一人と「こんなことができないか」と、相談が少しずつ舞い込むようになったのです。
「それは嬉しい誤算だった」と、島村氏と共にシステム構築を推進する、製造部主任補佐の田中氏は話します。「相談は既に4~5件は来ています。それらのニーズに対し、ローコード・ノーコードのプリザンターであれば、私たちでも簡単なツールを作ることや、教えることができるのが利点です」。実際、総務のセクションから依頼され、社内外で研修を受けた社員が提出する教育訓練報告書の電子保存にプリザンターを使うようになりました。また、医療機器の製造を担う技術部の社員に小一時間レクチャーをすると理解し、
必要なアプリは自分たちで作成するほど使いこなしております。「従来、デジタル管理ツールは一部の得意な人たちだけが使い、他の社員には浸透しなかったのが実態でした。プリザンターを使用することを引き金に潮目が変わり、今では、社員の間でDXへの関心が高まっていくのを肌で感じているところです。
プリザンターを起点として、できることからDXを開始するという姿勢で改善を実施していきたいと考えております。DXで社内のシステムを最適化していくことで、社内の業務改善の役に立ちます。そして、製品をよりタイムリーにお客様に届けられるようにして、お客様にももっと喜ばれるようにしていきたいです。」(田中氏)
今後の展望:プリザンターの活用をさらに進めるために社内体制を構築
認定パートナーのSMSデータテックを頼りに業務DXを推進
三幸製作所では、プリザンターをさらに活用するために次のステップに進もうとしています。一つは、現状、別サービスで行っている検査表データの入力を、プリザンターへ直にできるよう改修することです。「当初、入力フォーマットが変わって抵抗感が生じるのを防ぐため、別サービスによるワンクッションを入れましたが、プリザンターに直接入力することが本来の姿です。実現すれば、入力したデータをグラフに加工し、製品の安定稼働状況を製造部隊である技術部にリアルタイムでフィードバックすることも可能になります。然るべきタイミングで移行するために、今はその方策を考えている最中です」(池澤氏)。
もう一つは、製造業では不可欠な「BOM(Bill Of Materials:部品構成表)」と呼ばれる部品表のドキュメント管理にプリザンターを活用すること。プリザンターに、ある製品の名前を入力して検索すれば、製造するのに必要なBOMが一瞬で表示される仕組みを構想しています。「当社はBOMの管理体制が確立されてなく、そこをプリザンターでカバーしたいと考えています。既にテストで運用している段階です。少しハードルは高いですが、できることから実践している最中です。」(島村氏)
こうした業務の電子化を成し遂げるには、少し複雑になるため自分たちの力だけでは難しい面もあります。「だからこそ、頼れる存在がSDT」と、島村氏は言います。「SDTは仕事が緻密で、導入計画書も丁寧に作ってくれます。それは自分たちの理解を助けると同時に、稟議承認を得る際にも非常に有効な資料となっています。今後もSDTの力を借りながら、業務のDXを進めていければと考えています」(島村氏)
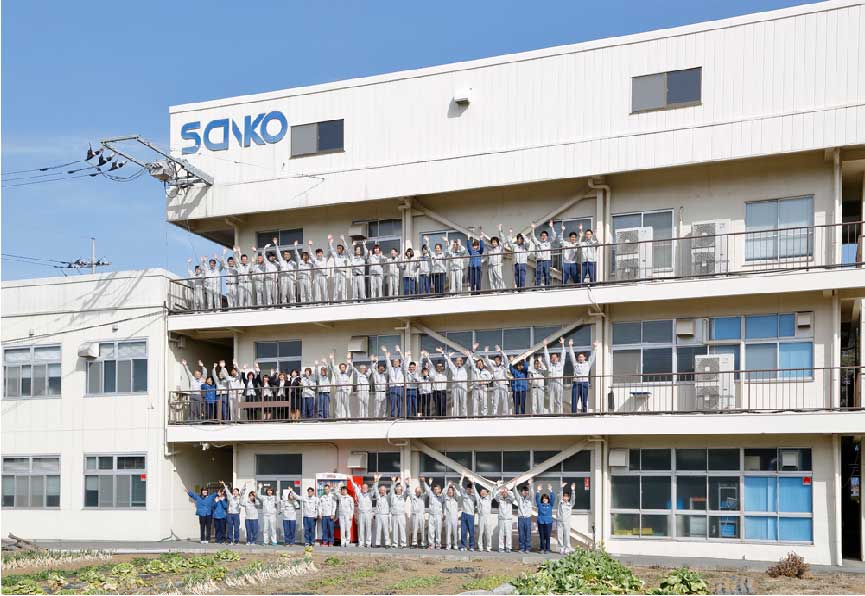
三幸製作所の社員の皆さま